Lean Six Sigma Prepares Professionals for Management Success
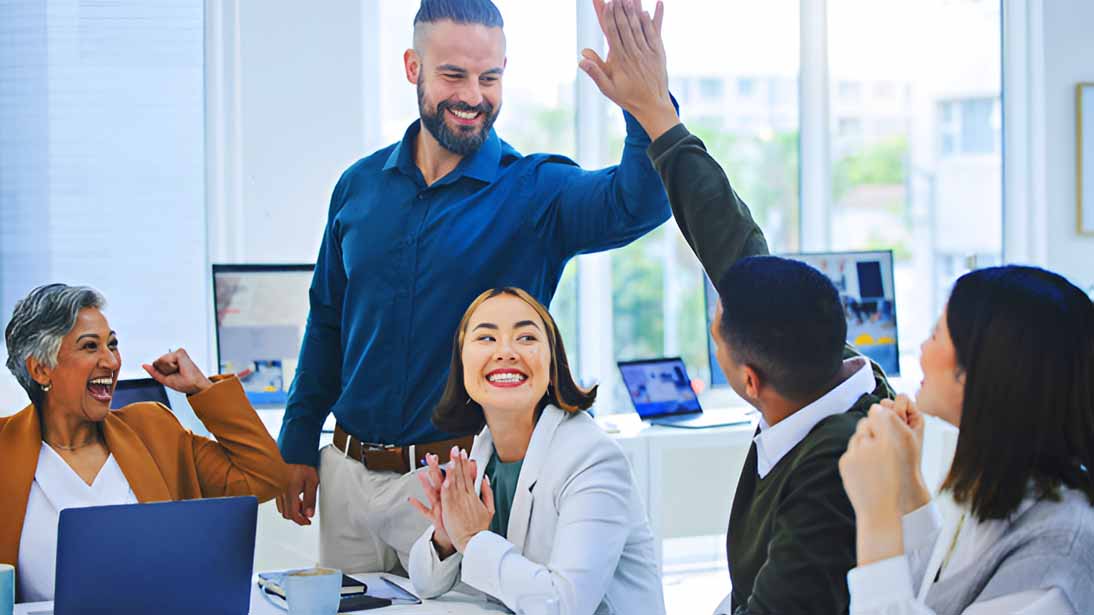
Lean Six Sigma training equips professionals with a powerful set of skills designed to improve business processes, enhance efficiency and reduce waste. Whether you're pursuing a beginner Six Sigma belt level or a more advanced belt designation, adopting Lean Six Sigma principles empowers you to become a leader in driving measurable improvements within your organization.
Professionals who earn Lean Six Sigma credentials learn to systematically solve complex problems. Beyond process improvement, Lean Six Sigma training also emphasizes critical thinking, data analysis and strategic decision-making.
As businesses focus on continuous improvement and operational excellence, Lean Six Sigma-trained professionals become valuable assets. They not only help organizations achieve cost savings and higher productivity but also contribute to creating a culture of innovation and sustainability. Their skills transfer across all industries, including manufacturing, healthcare and finance.
Key Skills Acquired in Lean Six Sigma Training
No matter what level of Lean Six Sigma training you achieve, you can develop expertise in the tools and techniques of the methodology. This includes the use of DMAIC (define, measure, analyze, improve, control) and finding and eliminating wasted actions in any type of process. This leads to a reduction in process variance that leads to errors and lower quality of products and services. You also learn data analysis, which is required to correctly apply many Lean Six Sigma tools.
You can also pick up skills in a variety of areas that make you more marketable to employers. They include the following.
Process Improvement
Lean Six Sigma training teaches you how to identify inefficiencies and implement improvements in business processes. By using structured methodologies like DMAIC, you can learn to analyze workflows, reduce waste and enhance quality. This leads to greater productivity and reduced costs.
Leadership Skills
Green Belts and Black Belts are often tasked with leading improvement projects. Lean Six Sigma training sharpens leadership skills by teaching you how to guide teams, including how to manage resources and motivate others. Effective leaders ensure the successful development and implementation of improvements.
Management Skills
Lean Six Sigma emphasizes project and time management. Practitioners learn to oversee projects from initiation through completion, ensuring they stay on track with deadlines, budgets and performance goals. These skills are crucial for aligning improvement efforts with broader organizational objectives.
Critical Thinking
Lean Six Sigma fosters critical thinking by encouraging data-driven decision-making. Professionals learn how to question assumptions, evaluate information objectively and use evidence to develop solutions. One of the tools of Lean Six Sigma – Five Whys – is specifically designed to help you find the root cause of a problem by continually asking ‘why’ questions. This analytical mindset is key to solving complex challenges.
Problem Solving
Learning how to systematically solve problems is a central tenet of the methodology. Every belt level within the Lean Six Sigma framework provides tools and techniques to break down problems and implement solutions. This problem-solving ability is essential in creating lasting, positive changes.
Communication Skills
Lean Six Sigma training reinforces the importance of clear, concise communication. Professionals must often explain complex data, methodologies and results to stakeholders with varying levels of expertise. Effective communication ensures alignment and buy-in from all team members and leaders, helping projects run smoothly.
Team Collaboration
Lean Six Sigma projects often require cross-functional collaboration, requiring professionals to work closely with individuals from other departments. This training enhances interpersonal skills, enabling participants to build relationships, share knowledge and work toward common goals.
The Benefits of Lean Six Sigma Training Across Industries
The key skills that people learn in Lean Six Sigma training apply across every industry.
For example, in manufacturing, Lean Six Sigma is used to achieve cost savings and higher-quality products by improving production processes. One example is General Electric, which famously used Six Sigma to streamline manufacturing processes and increase revenue. Six Sigma started in manufacturing, with Bill Smith introducing the methodology at Motorola in 1986.
In healthcare, hospitals have used Lean Six Sigma to improve how they manage patients as they move through the healthcare system, as well as how they organize processes like supply management within the hospital.
Lean Six Sigma can also help with risk management and process optimization in the finance industry. For example, management consultant Bain & Company helped a banking client better manage the credit application process, speeding it up and making it more accurate.
Technology companies also use Lean Six Sigma in a variety of areas. Microsoft has used Lean Six Sigma to improve customer service. Apple uses a Lean approach to inventory management. 3M has long been a proponent for Lean Six Sigma, including its benefits for sustainability.
Emory’s Lean Six Sigma Certificates
Emory Continuing Education offers five Lean Six Sigma certificate programs to help you take the next step forward:
- Lean Continuous Improvement
- Lean Six Sigma Yellow Belt
- Lean Six Sigma Green Belt
- Lean Six Sigma Green Belt for Healthcare
- Lean Six Sigma Black Belt
Lean Six Sigma training provides a path to unlocking new opportunities and career advancement. By emphasizing a mindset of continuous improvement, Lean Six Sigma prepares professionals for success in transforming organizations, keeping them competitive in the modern business world.
Learn more about the Lean Six Sigma programs in our portfolio by visiting our Area of Study page.