Engineer Prepares for Leadership with Lean Six Sigma Green Belt
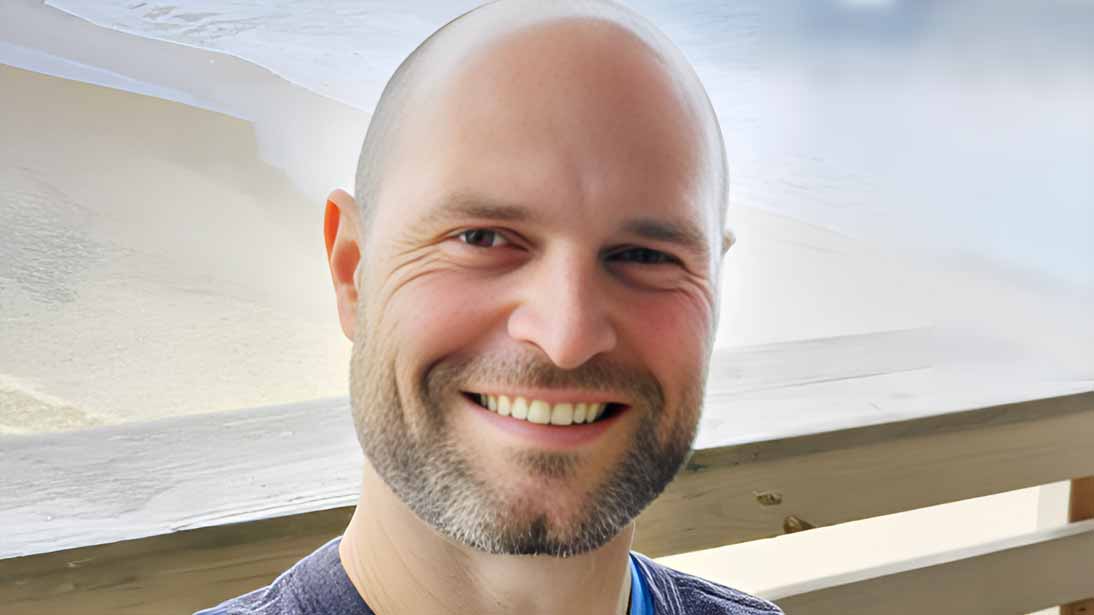
Before he completed Emory Continuing Education’s Lean Six Sigma Green Belt Certificate program, Douglas Thorn already had the skills to work as an engineer. But he knew he needed further education to achieve his goal of leading project teams and, ultimately, managing other engineers.
Thorn currently works as a Process Engineer II at LifeNet Health in Virginia Beach, Vir. Thorn said his day-to-day work involves qualifications of equipment and processes to help transfer new products into the production environment. He also works to improve processes by applying the tools and techniques of Lean Six Sigma.
“I find a lot of joy when I feel proud of the work that I’ve accomplished and when I’m able to pass on what I’ve learned to others,” Thorn said in a recent interview. “My personal goal is to make sure my professional path stays in this scope.”
His professional aspirations involve working where he manages others and helping guide them to achieve both individual and team goals.
“I enjoy the technical aspects of my job. However, I know there are others that are much better at this than I am that need guidance,” he said. “I feel I could make the biggest difference managing an engineering team.”
Before enrolling in the Green Belt program, he knew that professional development was key to achieving that goal. “Six Sigma is one of the largest programs used in industry, and I knew that if I wanted to get ahead in my career, that this was one program that I needed to understand,” he said.
Preparing For Project Leadership with a Lean Green Belt
Before earning his Lean Six Sigma Green Belt Certificate, Thorn earned a Bachelor of Science in Mechanical Engineering from the New Jersey Institute of Technology. While there, he was the college mascot, an experience he said provided “some of the most entertaining moments in my life.”
Thorn was introduced to Lean Six Sigma early in his career when he worked as a quality engineer in medical plastics.
“My boss had his Black Belt, and he would guide us through individual tasks using Six Sigma terminology. However, we never had the opportunity to follow the entire process,” Thorn said. “Even so, we were able to use control charts, determine root cause of issues, and create studies to help improve our process. Ever since this introduction I have known that I wanted to learn more about it.”
Thorn became interested in the Green Belt program because he wanted to close the gaps in his knowledge. He had spent a lot of time in the measure and implementation phases of Six Sigma but needed to understand more to achieve his goal of managing projects and people.
He said the program exceeded his expectations.
“The number of resources that were given to me from that class was extensive. The number of downloadable files for templates and instructions, PowerPoint slides, and others exceeded my expectations,” Thorn said. “I review them often as guidance.”
Biggest Takeaways from the Green Belt Program
Thorn credited Emory Lean Six Sigma instructor Mark Eclavea with speaking about and offering examples from his extensive work experience. Thorn said that Eclavea also offered guidance on what is important for managers to remember.
Thorn said he also was able to immediately apply what he learned in the Lean Six Sigma Green Belt Certificate program at work.
“My most valuable takeaway is understanding control charts more,” Thorn said. “A week after the class was over, I had an opportunity to help a department set up new control charts to watch weight differences over the last year as well as monitor it weekly. I couldn’t have done that without the class.”
Thorn also said he came away from the course with renewed appreciation for brainstorming.
“All types of brainstorming are fun,” he said. “Whether it is finding new projects or root cause, using affinity diagrams, silent brainstorming, multi-voting or others, it’s amazing the ideas that a team can produce.”
It’s also a concept he put to work while working with a group that brainstormed ideas for projects that summer interns could work on.
“We went from a list of about six projects to a list of 60,” he said. “We were then able to take them all and create an affinity diagram to further evaluate them and narrow it down to the top 10. It was fast, efficient and everyone was involved and excited.”
Advice For Those Considering the Green Belt Program
For those considering the Lean Six Sigma Green Belt program, Thorn said prospective participants should understand that it provides a foundation for intelligent and rational thinking, supported by using analytics and templates to make the best decisions.
He also noted that it works in every industry.
“My experience was for engineering; however, I had classmates that were in human resources, teachers and upper management who all gave notable examples of their work throughout the program that we were able to build on,” he said.
He added the program covers the Lean Six Sigma process “from the beginning to the end very well. I can assure you that you’ll use the items you’ve learned in your work immediately.”
He also said that the program offers strong support right from the beginning.
“It’s amazing how fast things happen when you ask for help. I was a bit lost about where I wanted to go and how much I could pay for. However, the moment I asked for guidance, the dream became a reality in days,” Thorn said. “Emory was an outstanding solution for me, and I highly recommend it to others.